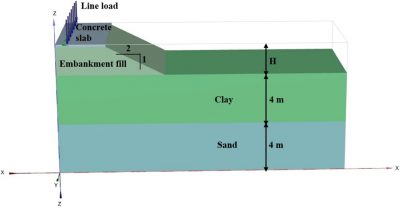
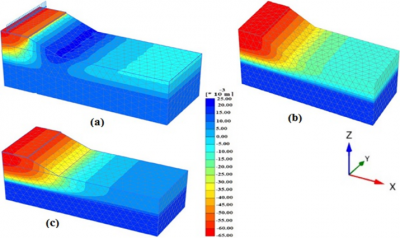
In the present study, an attempt has been made to understand the behavior of railway embankment through three-dimensional Plaxis software. The numerical modeling analysis was carried using four different backfill materials such as natural soil, 70% steel slag with 30% soil mixture, fly ash, and expanded polystyrene (EPS) geofoam with three different densities 12, 15 and 20 kg/m3. The comparative investigation of natural soil, steel slag-soil mixture, fly ash, and EPS geofoam as an embankment backfill materials were carried out based on stability and displacement conditions. The EPS geofoam is modeled as Mohr-Coulomb non-porous material. A panel of geofoam is placed immediately above clay soil during the construction phase of an idealized plane-strain railway embankment model. The magnitudes and distributions of static and dynamic load due to train on the embankment models with and without the geofoam panel are compared to quantify the reductions in applied pressure expected due to the placement of the geofoam material. Predicted magnitudes of vertical settlement and geofoam strains are also compared among cases studied in order to evaluate the effect of geofoam on embankment serviceability. Finite element simulation was performed to understand the effect of conventional and unconventional materials, and density of EPS geofoam backfill on vertical stress and settlements on the model embankment using Plaxis 3D software. The numerical analysis results indicate that soil-steel slag mixture has better strength and stability as compared to natural soil and fly ash fill. The analysis results revealed that placing geofoam above soft ground the embankment can reduce the maximum vertical stress and settlement depending on the geofoam thickness and density values. These findings point to a significant potential for using EPS geofoam to reduce the vertical thrust demand on soft ground and thereby increase their serviceability and their factors of safety against external instability.
Prof. J N Mandal