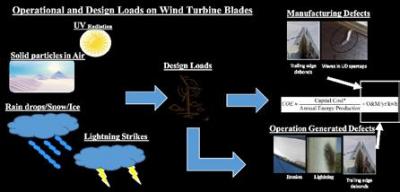
Composites have been extensively used in the manufacturing of wind turbine blades over the past two decades. Significant expertise and field experience has been accumulated in the design, manufacturing and repair / maintenance of these wind turbine blades. However, with the increasing blade length, the design imperatives have pushed the materials used for the blade construction from conventional E-glass to carbon fiber based polymer composites. This shift also leads to design shift from stiffness limited design to strength limited design. The strength limited design also comes with its own set of challenges with respect to manufacturability per design requirements and also the ability of designers to design per manufacturability. Similarly, defects induced during service need to be understood from their potential to cause catastrophic failure and in planning repair/maintenance of the affected components.
The research work being done in the group is aimed towards developing a physics based methodology to understand the defect causes in manufacturing process as well as develop a mechanics based analysis and strength prediction model to effectively predict the strength knockdown in various components due to the presence of defects. This information then would be used to develop a tool to decide on the criticality of defect for further disposition of the part. The utility of a physics based process for the disposition of the composite components with defects is in improving component reliability as well as guiding the development of realistic part tolerances for manufacturing. This will reduce the operations and maintenance costs as well as the manufacturing costs due to lesser repairs and scrap.
Prof. Chandra S Yeramalli