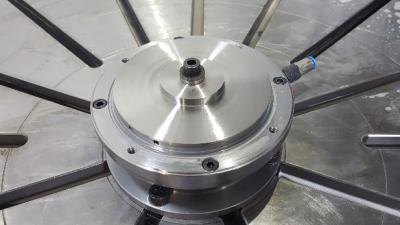
TMT (Thirty Meter Telescope) is one of the world’s largest ground based telescope project. The telescope’s primary mirror is 30 meters in diameter and is comprised of hundreds of hexagonal mirror segments. Each mirror segment is mounted on a critical support component known as the central diaphragm.
The central diaphragm is a thin-membrane disc shaped component made from Invar-36, an alloy of Iron and nickel known for its superior thermal expansion characteristics. The presence of high percentage of nickel in the alloy makes the workpiece very difficult to work with as it significantly affects tool life. Furthermore, as the component is extremely thin, it tends to distort after the process is complete due to stresses induced in the component during the process. The distortions violate the functional and geometric requirements as the component design imposes narrow tolerances on several of its geometric features. These aspects make the manufacturing process of the central diaphragm quite challenging.
At the National Centre for Aerospace Innovation and Research (NCAIR), we are involved in the development of the manufacturing process technology for the central diaphragm. This includes comprehensive characterisation of the workpiece material; optimised toolpath planning and cutting
tool selection for minimum induced stresses; fixture design for secure clamping of the workpiece during the manufacturing process; and optimised heat treatment stages for further reduction of induced stresses and distortion. Additionally as part of the technology development, several CNC machine systems and configurations are being
evaluated so as to make the manufacturing process flexible with wide outreach.
Currently the project is in its advanced stage of technology development and several prototyping activities are ongoing. On culmination, the technology will essentially build the capability with a systematic approach to manufacture extremely mission critical components with high precision and accuracy.
Prof. Asim Tewari