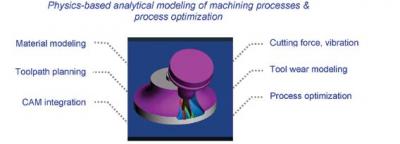
Precision machining is perhaps one of the most essential and widely performed manufacturing processes in several industries today, particularly in the aerospace and automotive sectors. It is amongst the few conventional manufacturing processes which ensure that raw materials are converted efficiently into functional components within the tolerance limits set by design. This is crucial in order to ensure optimal system performance. High technology sectors such as aerospace and defense widely use high grade steels, titanium, inconel and similar super-alloys to manufacture complex parts such as turbine blades, dies and molds with high precision. These materials, which possess excellent mechanical properties, are however difficult to process. This makes manufacturing a great challenge which as a result affects production and output and eventually the global supply-chain. Machining, particularly milling, is a highly dynamic process. The cutting forces generated during the process involve high-frequency fluctuations as the tool spins and engages the workpiece. These dynamic forces lead to tool vibrations which can affect surface quality and integrity of the component as well as cause dimensional inaccuracies in the finished part. At the National Centre for Aerospace Innovation and Research (NCAIR), we are developing an analytical physics-based milling process model to accurately predict cutting forces, torque and power, temperature, tool-wear and tool vibrations. This model integrates with a CAM (computer aided manufacturing) platform in which a workpiece material and the cutting tool can be simulated along a given toolpath to predict cutting forces and other performance parameters mentioned above. Based on the predictions, the cutting tool geometry, the toolpath and the machining process parameters can be optimised based on several criteria. This can result in reduced process cycle times and costs, more accurate finished parts, and improved surface quality and tool life.
Prof. Asim Tewari