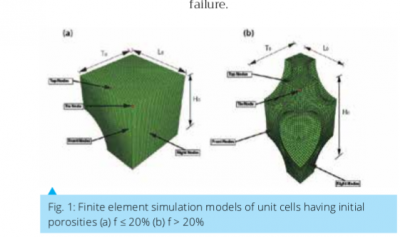
Bulk metallic glasses (BMGs) are amorphous alloys with enhanced properties such as high strength, large elastic strain, corrosion resistance, high fatigue and fracture toughness in comparison with their crystalline counterparts. This makes BMGs suitable for deployment in many applications. However, upon loading uniaxially beyond their yield point, most BMGs fail catastrophically, displaying very little plastic strain. This limits the use of BMGs in load bearing applications. Understanding failure mechanisms and developing methods to improve their properties has been of significant interest to researchers. The properties of monolithic BMGs are improved by introducing a secondary phase, such as a pore. Experimental investigations on porous BMGs and BMG foams show significant improvement in strain to failure.Our research group has analysed porous BMGs using the unit cell approach. The major assumption in this approach is that the distribution of pores within the material is homogeneous. This is a reasonable assumption referring to the experimental observations from literature. Fig. 1 shows the two types of unit cells, that are used to analyse (a) low porosity BMGs (f ≤ 20%) and (b) high porosity BMG foams (f > 20%). Anand and Su (2005) have proposed a large deformation, Coulomb-Mohr type constitutive model for elastic- viscoplastic response of pressure sensitive, plastically dilatants, and isotropic materials. This model has been used in the present study. The major findings from the present work are the mechanisms of deformation and failure in porousBMGs having pores of different sizes and shapes have been elucidated. The simulated stress-strain curves are found to be in reasonable agreement with the existing experimental results for a wide range of void volume fraction (or porosity, f). A comparison of stress strain curves for porous BMGs having wide range of porosities (2-60%) are shown in Fig. 2. For low porosity BMGs, the mechanism of deformation begins with nucleation of plastic strain around the pore diameter on loading beyond yield point. With further loading, the plastic strain spreads and localises to form shear bands. The mechanism of failure of low porosity BMGs involves linking of these shear bands with adjacent pores which finally leads to initiation of ductile cracking within the shear bands. A failed sample, compared with that obtained from the experiments from literature is shown in Fig. 3. For high porosity BMG foams, the mechanism of deformation involves reduction in porosity of the material, self contact of the pores, and their collapse on themselves causing densification of the material leading to apparent hardening in the stress– strain behavior. Different stages of deformation of a high porosity BMG foam is shown in Fig. 4. The present work could lead to development of better porous BMGs.
Prof. Parag Tandaiya