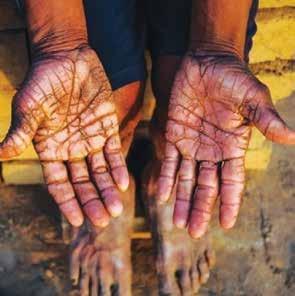
Brick manufacturing in India is a traditional and unorganised industry. Of late, due to rapid urbanisation, high rise metropolises and a spurt in real estate development, brick making has become one of the most flourishing and booming industries. There are more than 22,000 brick kilns in India engaging more than 3 million (30 lakhs) workers. The brick kiln industry is an unorganised sector in India where most of the jobs are performed manually. The process of brick making involves six major activities like mud preparation, moulding, carrying raw bricks to brick kilns, arranging raw bricks inside kilns for firing, firing of raw bricks and carrying out fired red bricks from brick kilns.
While performing the job, the workers suffer biomechanically, physiologically and psychophysically. The workers are also exposedto a high concentration of dust and temperature. The sustained awkward squatting posture adopted by the workers for more than 6 - 8 hours imposes severe musculoskeletal stress and is thereby likely to cause permanent musculoskeletal injury to the workers. The human body is not suited to this type of unnatural stress. As per our previous study, the average age of the brick kiln workers is 28 years and people beyond 40 years of age are seldom visible in these operations.
Our team has designed a new brick making process to improvise on occupational health, safety and the removal of drudgery by the ergo-design approach, in the traditional brick making industry.
So far, different types of moulds and a workstation concept have been designed to provide betterworking conditions and the ability to mould bricks in the standing position rather than sitting in a squatting position, which is not advisable. However, the team is yet to mechanise the process and make it more ergonomic and efficient.
The design and development of new methods, tools and instruments has been initiated which can help reduce the rigorous bending and lifting action of the workers while performing tasks such as moulding and transfer of bricks for drying and stacking. An attempt is being made to reduce the number of actions performed by the workers. Instead of moulding the bricks at one place and then transferring it for drying, the bricks could be moulded in the drying area. This will reduce the transfer element of the bricks, hence increasing the efficiency of the process.
Mr. Quashif Qureshi, a 2015 Tata Fellow is associated with ergonomics intervention in traditional brick making industry on removal of drudgery and developing safe work conditions towards enhancement of productivity.
New ergonomic prototypes have been made and tested in the field.
Prof. Gaur G Ray